Injection Plastic Mold Manufacturers: Pioneers of Innovation in Business
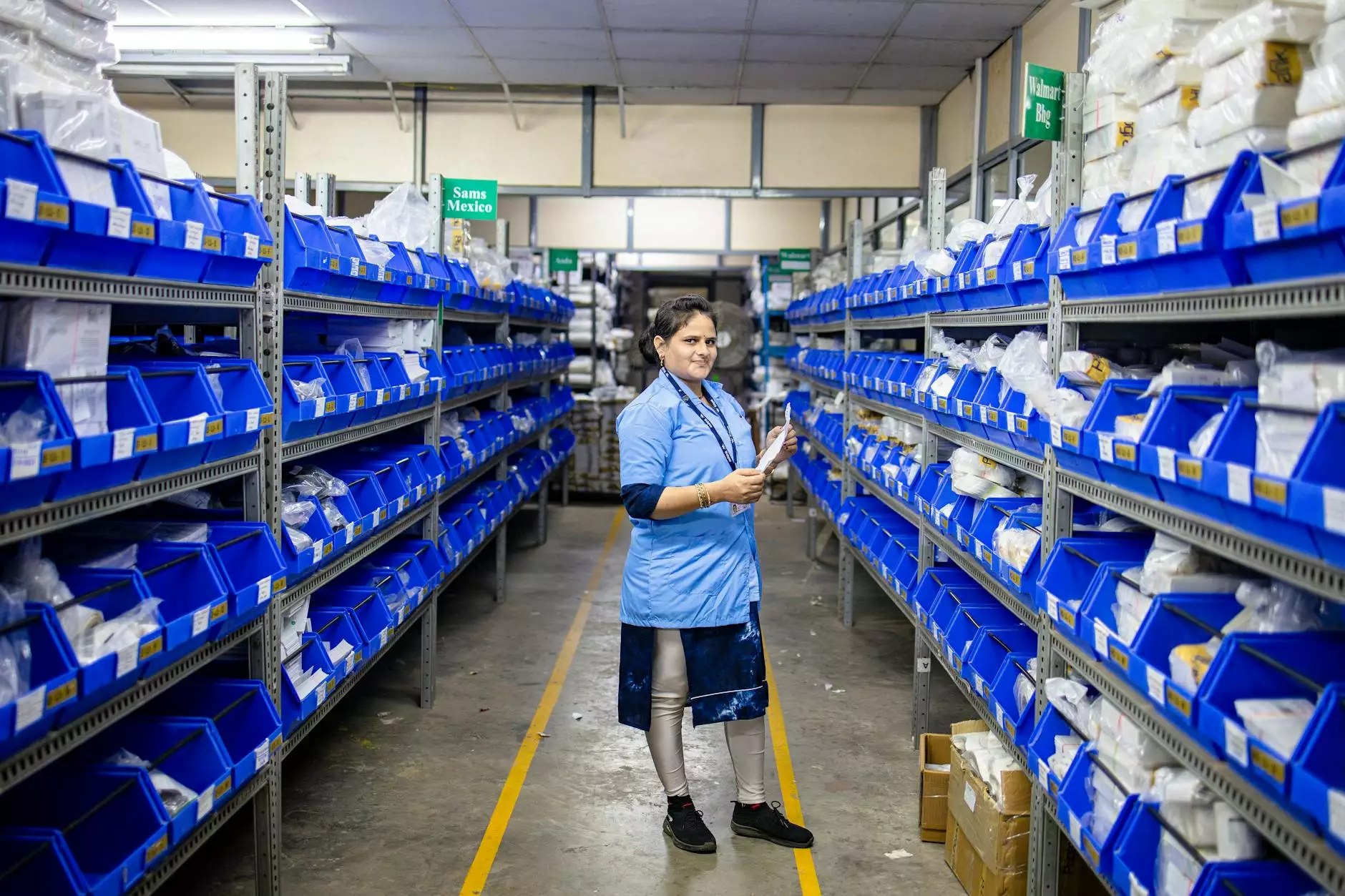
The world of injection plastic mold manufacturers plays a critical role in the business landscape today. With the rise of technology and manufacturing capabilities, these manufacturers have become cornerstone players in various industries, from automotive to consumer goods, electronics, and beyond. This article explores how these manufacturers contribute to business success, the intricacies of the manufacturing process, and why choosing the right partner is essential for quality and efficiency.
Understanding Injection Molding: The Backbone of Modern Manufacturing
Injection molding is one of the most efficient and versatile manufacturing processes used to produce plastic parts in vast quantities. The process involves:
- Heating Plastic Material: Raw plastic materials are heated until they become molten.
- Injecting the Material: The molten plastic is injected into a mold under high pressure.
- Cooling and Solidifying: Once injected, the material cools and solidifies into the desired shape.
- Removing the Molded Part: The finished product is then ejected from the mold.
Why Select Qualified Injection Plastic Mold Manufacturers?
The process of choosing an injection plastic mold manufacturer is not just about finding the lowest price. Here are several critical factors that emphasize the importance of selecting a qualified manufacturer:
1. Quality Assurance
A reputable injection plastic mold manufacturer prioritizes quality at every stage of production. They implement rigorous quality control measures, ensuring that each product meets industry standards and customer expectations.
2. Expertise and Experience
Manufacturers with extensive experience in the field can navigate potential challenges more effectively. Their knowledge of materials, design complexities, and production techniques can significantly impact the final output's quality.
3. Advanced Technology
Modern injection molding involves sophisticated machinery and techniques. Investing in manufacturers who utilize cutting-edge technology ensures precision and efficiency in the production process.
4. Customization Capabilities
Every business has unique needs. Qualified manufacturers have the ability to customize designs to suit specific requirements, enhancing product functionality and aesthetic appeal.
Key Industries Benefiting from Injection Plastic Molding
Injection plastic molding serves a wide array of industries. Here are a few key sectors where this technology plays an indispensable role:
1. Automotive Industry
In the automotive sector, light-weighting and fuel efficiency are critical. Injection-molded parts such as dashboards, bumpers, and components help manufacturers reduce overall vehicle weight while maintaining safety standards.
2. Electronics
From casings to intricate components, the injection plastic mold manufacturers facilitate the production of high-quality electronic devices that are lightweight, durable, and cost-effective.
3. Consumer Products
Everyday items, including toys, utensils, and household goods, are often made using injection molding. This allows for mass production of consistent quality products that meet consumer demands efficiently.
Steps in the Injection Molding Process
Understanding the injection molding process can help businesses appreciate the complexity and importance of this manufacturing technique. Here, we outline the key steps involved:
1. Design and Engineering
The journey begins with the design phase, where engineers create CAD (Computer-Aided Design) models of the components. This initial design will dictate the outcome of the entire production process.
2. Mold Making
The design is transformed into physical molds, usually made from steel or aluminum. The quality of the mold significantly impacts the end product’s precision.
3. Material Selection
The choice of plastic resin is crucial, as different materials offer varied properties such as strength, flexibility, and thermal resistance.
4. Production
The actual injection molding occurs in this phase, where the prepared material is injected into the molds over and over, yielding thousands of identical parts.
5. Finishing Touches
Once molded, parts undergo finishing processes like trimming, painting, or assembly to achieve the final desired product.
Cost Considerations in Injection Molding
The cost of injection molding can vary based on several factors. Companies must consider:
- Mold Design and Complexity: More intricate designs often require advanced molds, increasing costs.
- Material Costs: The type of plastic and its associated costs play a significant role in overall pricing.
- Production Volume: Higher production runs typically lower the cost per unit.
Future Trends in Injection Molding
The injection molding industry is continuously evolving, driven by technological advancements and market demands. Some key trends to watch include:
1. Sustainability
As industries focus on reducing their environmental impact, eco-friendly materials and recycling processes are becoming more prominent in injection molding.
2. Automation and Smart Manufacturing
The integration of automation and IoT (Internet of Things) in manufacturing processes is revolutionizing production, enhancing efficiency and reducing human error.
3. Innovative Materials
With ongoing research, new plastic materials are being developed to offer better performance, safety, and sustainability. These innovations open up opportunities for manufacturing stronger and lighter parts.
Choosing the Right Injection Plastic Mold Manufacturer
Selecting an injection plastic mold manufacturer requires careful consideration. Here are the essential steps businesses should follow:
1. Evaluate Experience and Portfolio
Look for manufacturers with a proven track record in your industry. Checking their past projects and client feedback can provide insights into their capabilities.
2. Consider Communication and Support
Effective communication is vital throughout the manufacturing process. Ensure that the manufacturer values client interaction and provides ongoing support.
3. Request Samples
Before committing to a manufacturer, ask for samples of their previous work. This will allow you to assess quality and craftsmanship firsthand.
4. Compare Costs
While cost shouldn't be the only deciding factor, it is important to find a balance between quality and affordability. Gather quotes from multiple manufacturers for comparison.
Conclusion: The Role of Injection Plastic Mold Manufacturers in Business Growth
In conclusion, injection plastic mold manufacturers are vital to the success of countless businesses across diverse industries. Their ability to produce high-quality, customized parts efficiently makes them indispensable in today's competitive market. By understanding the intricacies of the injection molding process, evaluating potential manufacturers, and considering future trends, businesses can harness the full potential of this technology to drive growth and innovation. At Deep Mould, we prioritize quality and customer satisfaction, ensuring our partners receive the best products for their needs. Together, we can navigate the challenges of modern manufacturing and pave the way for a successful future.